Kiln companies share the classification and characteristics of ceramic kilns
1. Classification of ceramic kilns
1. Divided by structure type: shuttle kiln, tunnel kiln, roller kiln, push plate kiln, round (turntable kiln), bell kiln
2. According to the heating method: coal kiln, wood kiln, electric kiln, gas kiln. Coal kilns and wood kilns have been eliminated, and clean energy kilns (electricity, gas) have reached a mature stage.
3. According to firing temperature: high temperature kiln, medium temperature kiln, low temperature kiln.
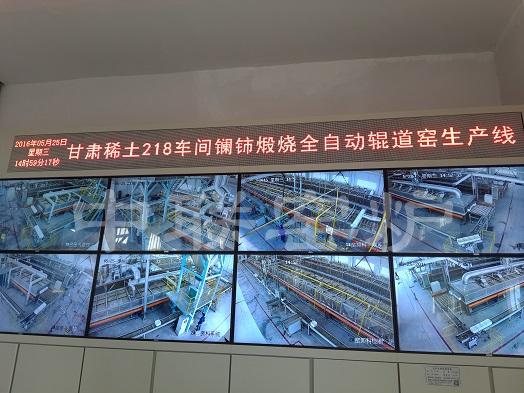
2. Introduction of Ceramic Kiln
1. Shuttle kiln: It is an intermittently fired kiln, similar to the structure of a matchbox. The kiln car advances into the kiln and fires it. After it is burned, it is pulled out and the fired ceramic is unloaded. The kiln car is like a shuttle, so it is called a shuttle kiln.
2. Tunnel kiln: It is generally a long straight tunnel with fixed walls and vaults on both sides and top, and a kiln car running on the track laid at the bottom. Combustion equipment is located on both sides of the middle of the tunnel kiln, forming a fixed high-temperature zone, burning zone, the high-temperature flue gas generated by the combustion flows along the tunnel towards the kiln head under the action of the chimney induced draft fan at the front of the tunnel kiln. The products entering the kiln are gradually preheated, and this section constitutes the pre-heat zone of the tunnel kiln. Cool air is blown into the kiln tail of the tunnel kiln to cool the products in the latter section of the tunnel kiln. The blown cold air flows through the products and is heated, and then drawn out and sent to the dryer as the heat source for drying the green body. This section constitutes the tunnel Kiln cooling zone.
3. Roller kiln: Roller kiln is a continuously fired kiln, a tunnel kiln that uses rotating rollers as a means of transporting billets. The ceramic products are placed on many closely spaced horizontal refractory rollers. The rotation of the rollers causes the ceramics to be transferred the kiln head to the kiln tail, so it is called a roller kiln.
4. Inverted flame kiln: The flames produced by combustion all go up the fire port of the combustion chamber to the top of the kiln. Because the top of the kiln is sealed, the flame cannot continue to rise. When there is no way to go, it is pulled down by the chimney's pumping force. After passing through the gap of the sagger column, it enters the branch flue the fire suction hole at the bottom of the kiln, and the main flue is finally discharged by the chimney.
5. Push plate kiln: also known as push plate tunnel kiln, it is a continuous heating and sintering equipment. According to the process requirements of sintered products, the required temperature zone and power are arranged to form the thermal part of the equipment to meet the product's heat requirement. demand. Put the sintered product directly indirectly on the high-temperature, wear-resistant push plate. The propulsion system moves the product placed on the push plate according to the product's process requirements, and completes the sintering process of the product in the furnace.
3. Selection of ceramic kiln
1. For the daily output below 20M3, and there are many types of products with different firing temperatures, since its own output is difficult to meet the production volume of the tunnel kiln, the rapid firing shuttle kiln is recommended.
2. For daily output equal to greater than 20M3, but its glaze color is complex, such as kiln changing crystalline glaze requires a certain constant temperature and cooling time, you can use a traditional shuttle kiln electric shuttle kiln; if the kiln variable glaze crystalline glaze is only part, you can choose Fast kiln, fast kiln is only fast, but also slow down. Slow, the temperature difference can be controlled very small. But the slow energy saving effect is poor.
3. For large output, high height, heavy weight, high temperature, single glaze color, trolley tunnel kiln can be selected. Such as high-temperature daily-use ceramics, bathroom ceramics.
4. For art ceramics, daily-use ceramics and bathroom ceramics with a temperature of less than 1300 ℃ and a large output, it is recommended to use a roller kiln a large-scale fast shuttle kiln.